What is Wax Emulsions?
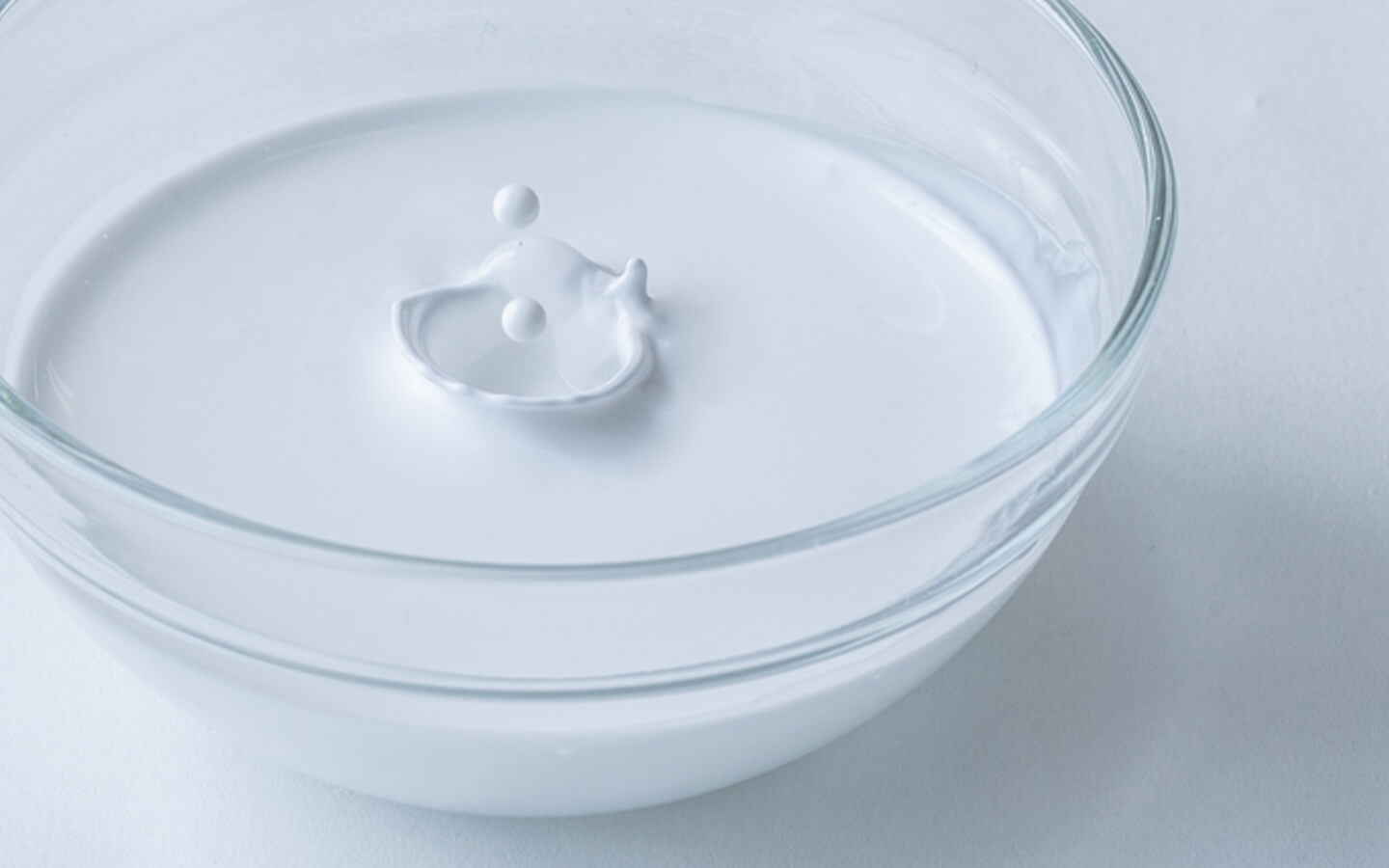
Relationship between emulsifiers and fields of use
Emulsifiers have both hydrophilic groups that have an affinity for water and oleophilic groups that have an affinity for wax.
It is important to select the appropriate emulsifier according to the type of wax and application.
For example, the anionic emulsifiers we use have excellent water repelling properties in the dried film due to the use of alkaline components that evaporate with moisture.
On the other hand, if a nonionic emulsifier is used, excellent mixing stability with various other emulsions can be achieved.
In addition, the dried film has excellent barrier properties and base material wettability.
In this way, selecting the appropriate emulsifier enables applications including mold release agents, polish, ceramic binders, powder metallurgy, lubricants, rust inhibitors, water repellents (including for food packaging), and paint additives.
Emulsification equipment
A general manufacturing process for wax emulsion involves pouring hot water into an emulsifying tank and then adding melted wax from a wax dissolving tank while stirring to create a preliminary emulsion.
Emulsifier should be added at the appropriate time.
After that, the particle size of the emulsion is adjusted using a high-pressure homogenizer, and the emulsion is cooled using a plate chiller and removed.
The high-pressure homogenizer has a very high shearing power and can adjust fine particle emulsions.
Even a small amount of emulsifier can be used to adjust the emulsion, without adversely affecting, for example, the water repelling properties, waterproofing, or heating stability, and without compromising the function of the base wax.
[Wax Emulsion]
EMUSTAR-0001 | EMUSTAR-042X | EMUSTAR-0135 | EMUSTAR-0136 | EMUSTAR-6315 | EMUSTAR-6315D | ||
---|---|---|---|---|---|---|---|
Wax Type | Microcrystalline Wax (Melting point: 84℃) |
Paraffin Wax (Melting point: 60℃) |
Synthetic Waxes (Melting point: 113℃) |
||||
Ionic | Anionic | Nonionic | Anionic | Nonionic | Nonionic | Nonionic | |
Nonvolatile (NSM-316) |
Wt% | 40 | 40 | 40 | 40 | 40 | 40 |
Viscosity (JIS K6833-11) |
mPa・s (At 20℃) |
25 | 12 | 12 | 14 | 20 | 1000 |
pH (JIS Z 8802) |
At 25℃ | 9 | 7 | 9 | 7 | 5 | 7 |
Particle Size | μm | < 0.5 | < 0.5 | < 0.5 | < 0.5 | < 0.5 | 4 |
[Form] | |||||||
Can | Net 17kg | ● | ● | ● | ● | ● | ● |
Drum | Net 190kg | ● | ● | ● | ● | ● | ● |
[Application] | |||||||
TTR | ● | ● | - | - | - | - | |
Polish | ● | ● | - | - | - | - | |
Binder (Ceramic, Powder metallurgy) | ● | ● | - | - | - | - | |
>Polish | ● | ● | - | - | ● | - | |
Slip agent | ● | ● | - | - | - | - | |
Rust prevention | ● | ● | - | - | - | - | |
Water repellent | - | - | ● | ● | ● | - | |
Ink additives | - | - | ● | ● | - | - | |
Ink additives (for anti-scratch) | - | - | - | - | - | ● | |
Release agent | - | - | ● | ● | - | ● | |
Release agent (TTR, Aluminum die-casting) | - | - | - | - | ● | - | |
Rust prevention | - | - | ● | ● | - | - |